- Insgesamt zählen zum Strukturentwicklungslabor zehn Testingenieure und 27 Werkstattmitarbeiter – hier ist ein Teil davon: (stehend, v.l.n.r.): Miroslaw Zieba, Daniel Mumme, Andreas Liebmann, Kai Kircher, Stefan Laick, Bernd Schad, Siegfried Schindler, Rainer Wenz, Stefan Schuch, Oliver heck, Francisco Steines Vieira; vorne, sitzend: Peter Taeny, Otto Hemmelmann
Ein „normales“
Fahrzeugleben –
das beziffern die Prüfer auf zehn Jahre Nutzungszeit oder
160.000 Kilometer
Fahrleistung.
Zeit ist relativ. Wie unterschiedlich schnell sie vergehen kann, lässt sich kaum anschaulicher erleben als im Strukturentwicklungslabor des Bereichs GME Vehicle Development im Internationalen Entwicklungszentrum (ITEZ) in Rüsselsheim. Ein Blick in den Türzuschlag-Prüfstand: Da thront ein Opel-Prototyp, dessen Türen sich öffnen und schließen, immer und immer wieder, vorne wie hinten, von mechanischen Armen bedient, die mit genau definierter Kraft und Geschwindigkeit arbeiten, extrem kurz, aber exakt getaktet – als betrachte man einen Film im Zeitraffer.
Und im Prinzip soll die Tür-Tortur auch nichts anderes sein. Denn der Test lässt die Schließmechanismen an der Opel-Karosserie die Belastungen erfahren, denen sie „draußen“ in einem kompletten, normalen Fahrzeugleben ausgesetzt sind. Drum heißt es: Tür auf, Tür zu, Tag und Nacht, sieben Tage die Woche, bis zu vier Wochen lang…
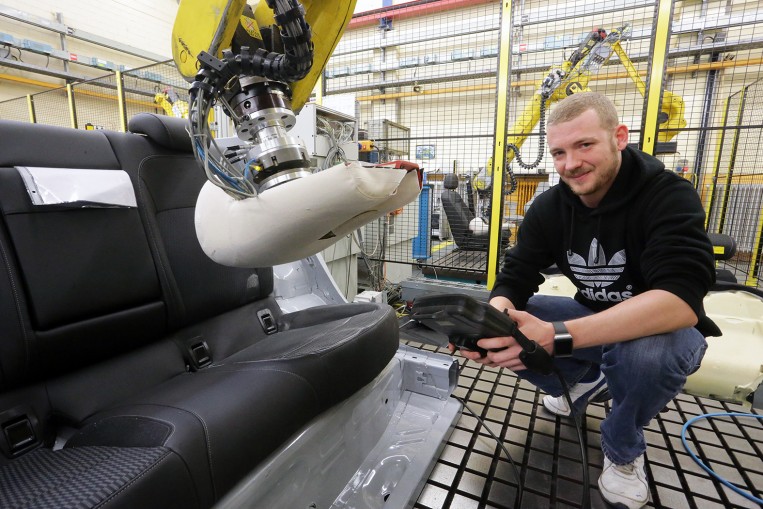
Sitzt auch alles? Tobias Friedrich checkt den Prüfstand, bevor die Testreihe beginnt.
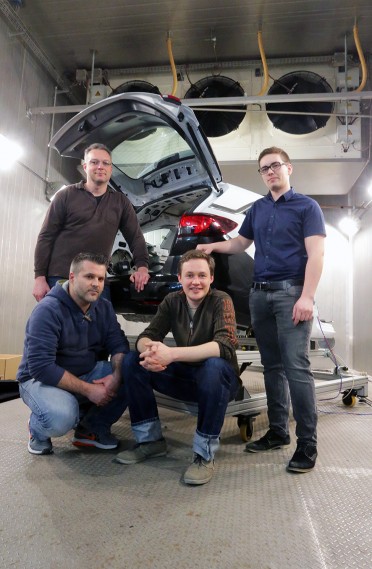
Wenn sie Türen knallen lassen, tun sie’s nur zu Testzwecken: (v.l.) Bernd Schad, Oliver Heck, Siegfried Schindler und Francisco Steinnes-Vieira.
ZEHN JAHRE NUTZUNG ODER 160.000 KILOMETER
An diesem Prüfstand wird sogar das 1,6-fache einer durchschnittlichen automobilen Lebenserwartung simuliert – „und für Heckklappen und Motorhauben setzen wir sogar den Faktor 1,83 an“, erklärt Versuchssachbearbeiter Siegfried Schindler, der die Versuchsreihe gemeinsam mit Techniker Oliver Heck betreut. Damit Opel-Fahrer sicher sein können, dass die Wagentüren auch am letzten Tag noch so schließen wie am ersten.
Ein „normales“ Fahrzeugleben – das beziffern die Prüfer auf zehn Jahre Nutzungszeit oder 160.000 Kilometer Fahrleistung. Die Tests zu dokumentieren, auszuwerten, Ergebnisse und Erkenntnisse an die beauftragenden Abteilungen zurückzumelden – „das ist sehr spannend“, sagt Francisco Steinnes-Vieira, der mit 24 Jahren der jüngste Versuchsingenieur im zehnköpfigen Team von Otto Hemmelmann, Lead Engineer Test Methods, ist. Er hat bereits ein Berufspraktikum im Strukturentwicklungslabor absolviert, seine Bachelorarbeit hier verfasst und ist nach erfolgreichem Studienabschluss nun fester Bestandteil der Testtruppe im Gebäude P10.
ARBEITSKLIMA KANN WECHSELN: VON MINUS 40 BIS PLUS 80 GRAD CELSIUS
Aktuell betreut Steinnes-Vieira eine Versuchsreihe in der Klimakammer des „Slam“-Testbereichs. Auch hier heißt es permanent Tür auf, Tür zu, aber unter ständig wechselnden äußeren Bedingungen: Die Anlage kann minus 30 Grad Celsius Kälte ebenso simulieren wie plus 80 Grad Hitze oder eine Luftfeuchtigkeit von 95 Prozent. „Hier sieht man jeden Tag, für was wir Entwicklungsarbeit leisten“, beschreibt Steinnes-Vieira, was ihn an seinem Job so begeistert. Da vergeht die Zeit wie im Flug…
Was die Klimakammer des „Slam“-Testbereichs an einer einzelnen Tür leistet, lässt sich im P10 auch an einem kompletten Fahrzeug exerzieren. Der Wärme- und Kälteprüfstand erlaubt jedoch nicht nur Temperaturwechseltests zwischen minus 40 und plus 80 Grad Celsius bei unterschiedlich definierter Luftfeuchtigkeit, sondern auch Prüfungen bei laufendem Motor im Straßeneinsatz, der mit Hilfe der integrierten „Vier-Stempel-Anlage“ simuliert werden kann. Sogar die Fahrbahnqualität lässt sich variieren.
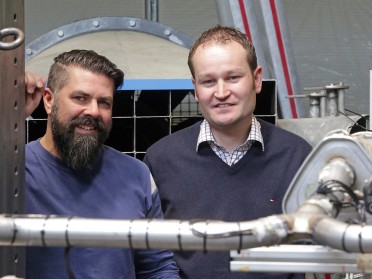
Dampf ablassen? Ist im Abgasanlagenprüfstand Tagesgeschäft – Stefan Schuch und Alexander Schmidt sorgen dafür, dass alles nach Plan läuft.
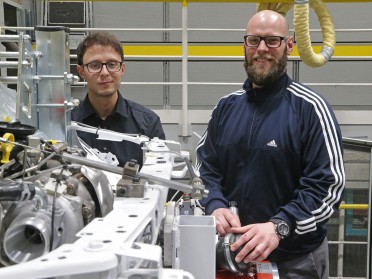
Shakin all over: Kai Kircher und Peter Taeny testen im „Shaker“, dass die Motoraufhängung auch dauerhaft hält, was Opel verspricht.
„Wir können auch Ein- und Ausstiegsszenarien simulieren und dabei die Fahrgastdaten variieren – vom 1,80 Meter-Normalo bis zum stark übergewichtigen Sitzriesen“
– Tobias Friedrich –
TESTFAHRER UND LABORTESTER STIMMEN SICH AB
Komplette Fahrzeuge werden auch auf dem 26 Kanal-Ganzfahrzeugsprüfstand auf Herz und Nieren getestet. Hier liegt der Fokus auf der Dauerhaltbarkeit von Karosserie und Chassis, entsprechend „bewegt“ ist das kurze, aber intensive Leben, das der Prototyp in dieser Kammer führt. Klar: „Belastungstests mit diesem Anspruch werden auch auf den Spezialstrecken im Opel Test Center Rodgau-Dudenhofen gefahren“, erzählt Versuchsingenieur Kai Kircher. „Die Testfahrer benötigen allerdings drei bis vier Monate, um ein komplettes Fahrzeugleben abzubilden – wir schaffen das auf unseren rund um die Uhr brummenden Prüfständen in einem Drittel der Zeit.“ Selbstverständlich verstehen sich Labortester und Testfahrer nicht als Wettbewerber, im Gegenteil: „Wir gleichen unsere Ergebnisse regelmäßig miteinander ab, was uns zu wichtigen Erkenntnissen führt, wie wir in unseren Anlagen noch realere Bedingungen schaffen können.“
„SHAKEN“ ODER BOXEN? MATERIAL WIRD AUF VIELE ARTEN STRAPAZIERT
Ganz schön geschüttelt, aber nicht gerührt wird derweil am „Shaker-Tisch“, allerdings kein Martini, sondern ein neues Opel-Aggregat: Die Tester konzentrieren sich dabei auf die dauerhafte Belastbarkeit der Motor- und Getriebeaufhängung. Die Qualität des Aggregats checken die Kollegen von Powertrain in eigenen Tests.
An einem anderen Prüfstand prügelt ein mit einem überdimensionalen Boxerhandschuh bewehrter Roboterarm auf Sitzbezüge und -Schäume ein, um die Dauerhaltkeit eines Opel-Sitzes zu testen. „Wir können auch Ein- und Ausstiegsszenarien simulieren und dabei die Fahrgastdaten variieren – vom 1,80 Meter-Normalo bis zum stark übergewichtigen Sitzriesen“, erklärt Tobias Friedrich, der vor kurzem seine Technikerausbildung abgeschlossen hat.
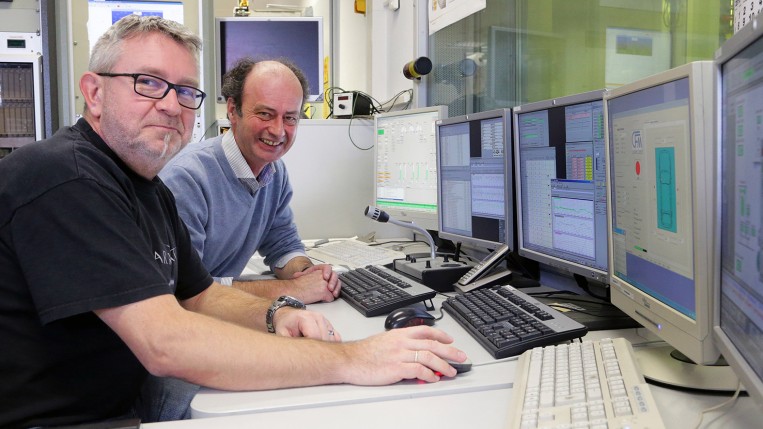
Sie freuen sich über ein gutes Arbeitsklima – im Prüfstand und davor: Rainer Wenz und Otto Hemmelmann.
„Unsere Versuchsreihen
begleiten mittlerweile den gesamten Fahrzeugentwicklungsprozess.“
– Otto Hemmelmann –
DIE ZEIT STEHT NIEMALS STILL
Seit 2001 sind die Prüfanlagen im Body Lab in Betrieb. Stehengeblieben ist die Zeit seitdem nie, schließlich müssen die Testeinrichtungen mit der permanenten technischen Weiterentwicklung der Opel-Fahrzeuge Schritt halten. „Dass wir beispielsweise auch mal die elektronische Steuerung einer Heckklappe prüfen müssen – auf die Idee wäre vor 20 Jahren noch keiner kommen“, schildert Otto Hemmelmann.
Doch auch die Zahl der internen Auftraggeber wächst und lässt die Aufgaben immer vielfältiger und anspruchsvoller werden. „Unsere Versuchsreihen begleiten mittlerweile den gesamten Fahrzeugentwicklungsprozess“, erklärt der Leitende Ingenieur. In der Praxis bedeutet das: Sobald Visionen eines Opel virtuell in „Computer Aided Design“ (CAD)-Programmen entstehen, können die Simulationsspezialisten bereits auf Daten zurückgreifen, die im Strukturentwicklungslabor erhoben worden sind. Während des Produktentwicklungsprozesses müssen immer wieder einzelne Komponenten getestet werden, die sich zunehmend komplexer präsentieren. Und kurz vor dem Start der Serienfertigung stehen Validierungstests der kompletten Fahrzeuge an.
Da braucht es sorgfältige Vorausplanung – und ein ausgeklügeltes Zeitmanagement. Denn ein ganzes Fahrzeugleben in vier Wochen abzubilden, mag verdammt kurz sein, andererseits können vier Wochen, die ein Prüfstand belegt ist, ziemlich lang werden, wenn andere Aufträge in der Warteschleife hängen. Zeit ist eben relativ – erst recht im Strukturentwicklungslabor.
Stand Februar 2016