- Das Zeit- und Weganalysen-Team (v.l.n.r.: Manuela Bartonek, Franz Peiritsch, Dieter Holzmaier, Thomas Strasak, Herbert Feindert, Paul Schachinger).
- Jedes Detail ist wichtig (Herbert Feindert, Manuela Bartonek).
- In der Lagerlinie werden pro Jahr circa 90.000 Tonnen an Lasten bewegt (v.l.n.r.: Manuela Bartonek, Paul Schachinger, Dieter Holzmaier).
- Vom Lkw bis zum E-Trolly – jeder Logistik-Vorgang wird genau analysiert (Dieter Holzmaier).
Im März 2013 starteten die Werkslogistiker ihr erstes KVP-Projekt, das sich mit Zeit- und Weganalysen befasste. Bis Februar 2015 erhöhte sich die Zahl der abgeschlossenen Projekte auf sechs; ein siebentes ist zurzeit noch in Arbeit. Alle mit ähnlich verblüffenden Erfolgen. Rund 2.000 Kilometer pro Jahr konnten an Wegstrecken eingespart werden. Und noch wichtiger: Die MitarbeiterInnen schaffen jetzt in kürzerer Zeit die gleiche Arbeit.
Wie ein Uhrwerk
Wie kann das nur gehen? Das Geheimnis liegt zunächst im Anwenden bewährter Methoden – wie sie schon seit Jahren in den Produktionsbereichen erprobt wurden: Alle Arbeitsplätze eines Bereiches werden akribisch erfasst und die Zeitdauer der einzelnen Arbeitsschritte vermessen sowie alle Erhebungsdetails in Pillar-Charts dargestellt. Danach werden in vielen kleinen Schritten ergonomische Verbesserungen ausgetüftelt und die Situation vorher und nachher gegenübergestellt.
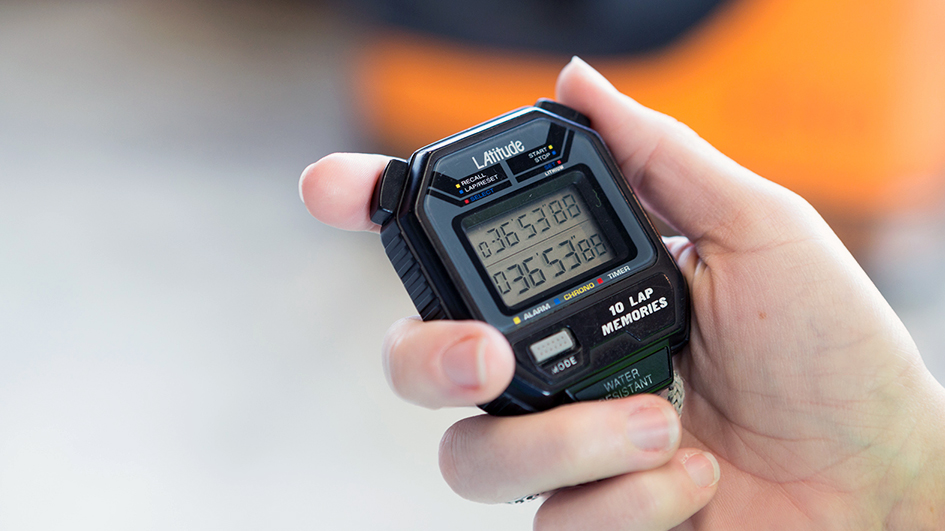
Exakte Zeitmessungen gehören dazu.
Wenn es um Logistik-Prozesse geht, wird die Sache noch einmal komplizierter: Im Motorbau zum Beispiel kurven sechs Staplerfahrer und zwei Loop-Fahrer herum, um Rohteile in die Produktion zu liefern und Leergut wieder abzuholen. Je nach den Stationen beziehungsweise Stopps, die angefahren werden müssen, ergeben sich unterschiedliche Wegstrecken. Loop 1 zum Beispiel hat 11 Stopps und befördert dabei je Fahrt 272 Kleinlastträger/KLT. So ergibt sich eine Wegstrecke von 924 Metern. Loop 2 hat zwar nur 10 Stopps und nur 232 KLT zu befördern. Trotzdem beträgt die Wegstrecke 1.176 Meter. Die Loops fahren im Stundentakt. Das ergibt 16 Loops je Schicht. Wer also Logistikprozesse verändern will, muss wie ein Uhrmacher handeln – jedes Rädchen der Abläufe muss haargenau in die anderen greifen.
Ergonomie und Arbeitssicherheit
Katrin Grandl/Manager Material Handling & Packaging beschreibt die Verbesserungen im Detail: „Lagerorte wurden geändert oder andere Anstell-Abläufe entwickelt. Im Vordergrund standen dabei immer ergonomische Überlegungen und Aspekte der Arbeitssicherheit.“ Musste zum Beispiel der Loop-Fahrer bisher das KLT über das laufende Montageband hinweg heben, um es anstellen zu können, so erfolgt der Anstellvorgang nunmehr auf „direktem“ Wege. Das ist ergonomisch günstiger und zeitsparender. Oder die Wareneingangskontrollwaage bekam einen anderen Platz, so dass der Stapler-Fahrer nun leichter – und auf kürzerem Wege – zufahren kann. Das Vermeiden von unnötigen Umwegen steht überhaupt bei den Zeit- und Weganalysen im Vordergrund. Geradeaus fahren statt im Zickzack ist eben bequemer und zeitsparender, also summa summarum effizienter.
Als besonders erfolgreich erwies sich das KVP-Projekt „Die m2-Sucher“, das im F 17-Getriebebau angesiedelt war. Je Schicht konnten 3,5 Stapler-Fahrtkilometer eingespart werden, eine etwa 300 m2 große neue Lagerfläche wurde geschaffen und zahlreiche Teilenummern umgelagert.
Perpetuum mobile
Bei jedem der bisherigen KVP-Projekte ergaben sich weitere Ziele und Visionen, wie: Die Linienanstellung sollte noch weiter verbessert werden. Oder: Wenn wir Dollys statt Staplern einsetzen, können wir noch effizienter werden. – Das Verbessern hört also nicht auf.
Katrin Grandl bringt ihre Zukunftsvision für die Werkslogistik auf den Punkt: „Die bisherigen Zeit- und Weganalysen haben uns gezeigt, dass wesentliche Verbesserungen möglich sind. Diesen Weg wollen wir weiter verfolgen: weil diese Maßnahmen die Arbeit für die Mitarbeiter angenehmer machen und darüber hinaus die Produktivität steigern.“
Text: Kristin Engelhardt, Fotos: Stephan Huger
13 Stapler,
10 E-Trollys
Pro Jahr im gesamten Werk zurückgelegte Kilometer:
circa 235.000 km. Das entspricht fast sechs Erdumrundungen.
In der Lager-Linie pro Jahr bewegte Lasten:
circa 90.000 Tonnen.
Pro Schicht arbeiten im Bereich Material Handling:
7 MitarbeiterInnen im F 17-Getriebebau,
7 MitarbeiterInnen im M 20/32-Getriebebau und
10 MitarbeiterInnen im Motorbau.