- Das Projektteam M 20/32-Value Pack.
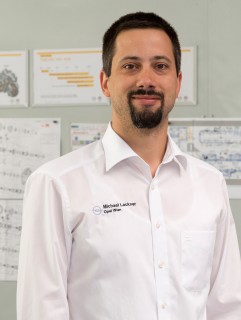
Michael Lackner/M 20/32-Launch Manager und Leiter Manufacturing Engineering.
Ein Sechsgang-Getriebe besteht aus bis zu 180 Einzelteilen. Und weil bei Getrieben ein Rädchen ins andere greift, sind bei Getriebe-Designänderungen im Dienste der Qualität meist sehr viele Einzelteile betroffen. Im speziellen Fall 80 Einzelteile. Drei Wellen, sieben Gangräder (von insgesamt elf), Dichtelemente, Schaltelemente, der Schaltmechanismus – um nur einige der wichtigsten Teile zu nennen – zählten dazu.
Was das Getriebeprojekt noch einmal extra-spannend machte, war die Vielzahl der Varianten, die berücksichtigt werden musste. M 20/32-Launch Manager und Leiter des Manufacturing Engineering-Teams Michael Lackner erklärt: „Während des gesamten Projekts mussten wir alle aktuellen 133 Typen des Sechsgang-Getriebes fertigen.“ Es mussten ja sowohl die Getriebe, die durch neue Varianten abgelöst werden sollten, als auch die neuen Getriebe produziert werden.
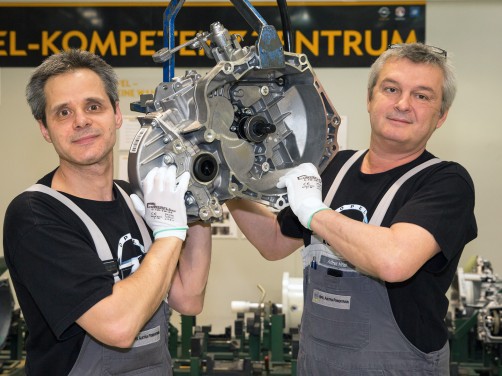
Karl Lippert (l.) und Alfred Hriza fertigten die Prototypen.
Seit Beendigung des Projekts werden statt der bisherigen 87 Generation 2-Sechsgang-Getriebe-Varianten nur mehr 46 neue, verbesserte M 20/32-Getriebe-Typen gefertigt. Die bisherigen fünf Allrad-Varianten wurden durch fünf neue Allrad-Varianten in verbesserter Bauweise ersetzt.
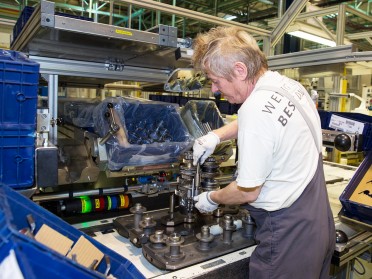
Harald Kemminger.
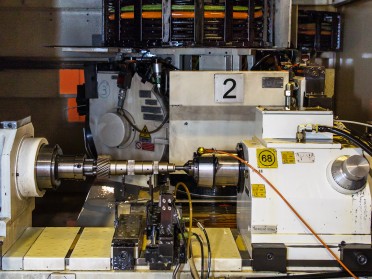
Tachella-Schleifmaschine zum Einstich-Schleifen.
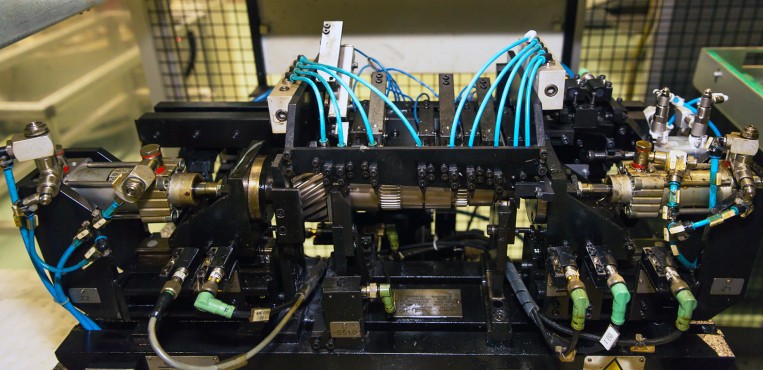
Messen der geschliffenen Einstiche.
„Ein Getriebe muss extrem robust sein und soll gleichzeitig nichts wiegen sowie nur ganz wenig kosten.“
– Michael Lackner –
Werte-Huckepack
Das Motto lautete „Value-Pack“. Die im Design veränderten neuen Getriebe bekamen sozusagen ein Wertpaket verpasst. Mit ausgeklügelten Verbesserungen wie zum Beispiel einer asymmetrischen Kupplungsverzahnung, die Zahn-auf-Zahn-Stellungen verhindert, und Gewichtsoptimierungen. Klingt leicht, ist es aber nicht. Lackner erklärt: „Ein Getriebe muss extrem robust sein und soll gleichzeitig nichts wiegen sowie nur ganz wenig kosten.“
Doch Rüsselsheimer Designer, Asperner Planer und alle MitarbeiterInnen in den betroffenen Produktionsbereichen schafften das Kunststück. Seit 11. Jänner 2016 werden die neuen, verbesserten M 20/32-Getriebe in alle Welt ausgeliefert. Michael Lackner beschreibt die Etappen, die dahin führten, im Rückblick: „Erste Designvorschläge gab es Anfang 2013, die tatsächlichen Änderungen wurden im November 2013 festgelegt. Gleichzeitig wurde der Terminplan für die notwendigen Umbauten in der Produktion entworfen. Fast alle Fertigungsbereiche waren in irgendeiner Form betroffen. Ab Sommer 2014 wurde umgebaut, in der Montage, in der Wellenfertigung, in den Gangräder-Linien … In diesen Bereichen blieb fast kein Stein auf dem anderen. Die geänderten Synchronwinkel zwischen den Gängen galt es zu berücksichtigen, neue Drehprogramme zu implementieren u.s.f. Und vor allem mussten alle zugehörigen Messmittel und Dokumente – von der Arbeitsanweisung bis zur Risikoanalyse – angepasst werden.“
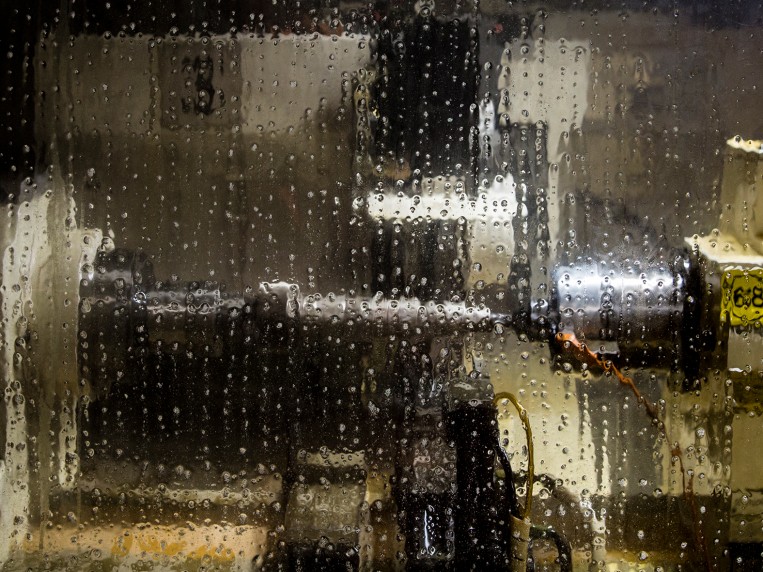
Gefertigt wird mithilfe von Öl-Wasser-Emulsionen.
„Ich muss schon sagen, auf mein Team bin ich ganz besonders stolz. “
– Michael Lackner –
Prüfmarathon
Als besondere Herausforderung entpuppten sich die vielfältigen Prüfungen, die die Getriebe durchlaufen mussten. Wöchentlich wurden fünf bis zehn für Qualitätstests bestimmte Prototypen von zwei eigens dafür abgestellten Montage-Mitarbeitern hergestellt, im Prüfstand der Qualitätsabteilung getestet und danach an weitere prüfende Stellen versandt; für den Dauertest, den Kalttest, den Getriebe-Prüfstand, den Einsatz in einem Crash-Fahrzeug, weitere Checks in der Entwicklungsabteilung …
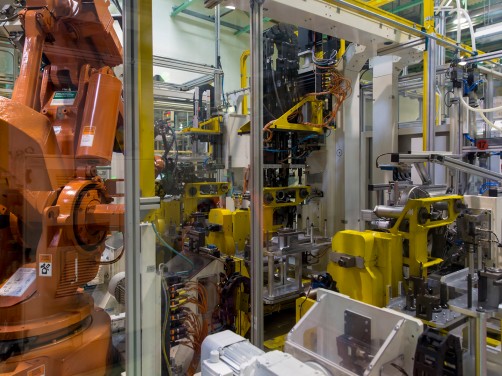
Verschrauben der Schalteinheit.
Insgesamt 250 Prototypen durchliefen das aufwändige Procedere. Lackner sagt dazu: „Wenn es um die Qualität unserer Produkte geht, sind wir bereit, jede Mühe auf uns zu nehmen. Alle an dem Projekt Beteiligten haben da wirklich Herausragendes geleistet.“ Und fügt hinzu: „Ich muss schon sagen, auf mein Team bin ich ganz besonders stolz. Manufacturing Engineering ist projektverantwortlich, ist die treibende Schnittstelle zwischen Produktion und Maschinenhersteller sowie der Zentrale in Rüsselsheim. Dieser Aufgabe muss man unter allen Voraussetzungen gewachsen sein; mit dem übergeordneten Ziel: bessere Getriebe für unsere Kunden herzustellen.“