The high-speed milling machines have five axes. The workpiece is stationary. Only the tip whirls about.
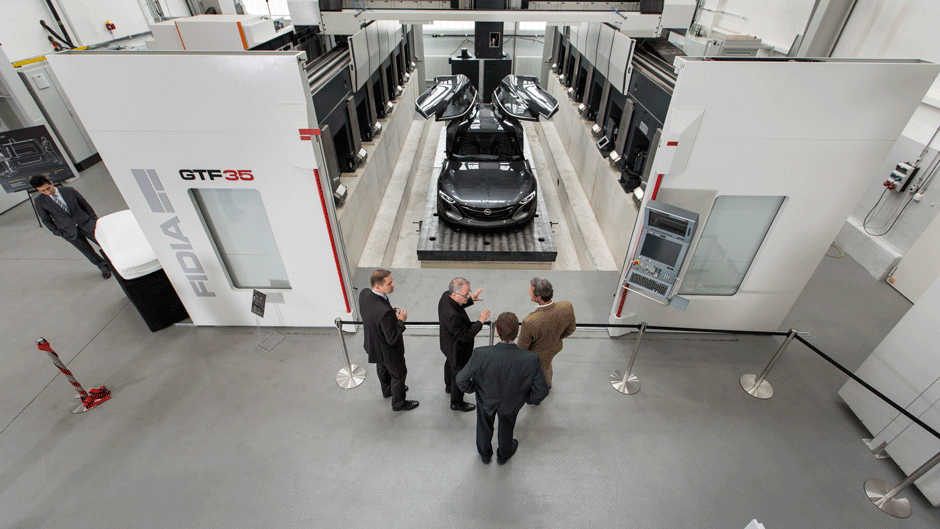
Opening of the new center: the Monza concept vehicle displayed at the IAA by design experts was set inside the new high-speed milling system.
From left to right. Stopping. Back to the starting position. Zigzagging to the top left and then everything over again, the hard metal tip romps just like a puppy. Brown hard plastic shavings fly through the air. A quiet whirring can be heard. The choreographer of the daring movements behind the glass screen is Stefanie Duinker. The 23-year-old CNC operator programmed the high-tech milling machine that’s handling the workpiece. With every new movement, the data relating to the axis radii change on the control unit’s display screen. The milling-machine operator strips away material one movement at a time. Slowly you can make out the chosen characteristic lines and perfect curves on the clamped workpiece.
FETCHINGLY DEVELOPED, SUBTLY IMPLEMENTED
“The roofline is particularly nifty, featuring at first the semi-circle shape typical of a classic coupé. Then just before the hatch it rises slightly,” Stefanie Duinker explains, as the tip of the milling machine begins to handle the workpiece from above. Duinker is one of 22 employees at the center for high-speed milling at the Rüsselsheim plant. The design models and concept vehicles will be formed in future in this center. It was officially opened on May 7. The red ribbon was ceremoniously cut by GM Director of Global Design Operations Mark E. Leavy, GM Executive Vice President & President Europe Dr. Karl-Thomas Neumann, Vice President of Design Mark Adams, Design Operations Director Richard Bolz, as well as Head of Opel Works Council Wolfgang Schäfer-Klug.
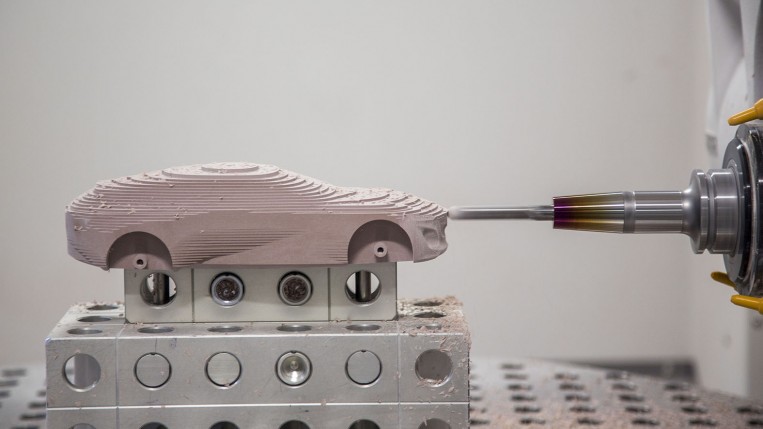
The rotary cutting tool strikes the clamped workpiece: moving up to 60 meters per minute, the hard metal tip of the milling machine works on the model – here that of a Monza concept.
← 22 employees work at the new milling center. Kristina Schell operates the mini mill, a milling machine for metal.
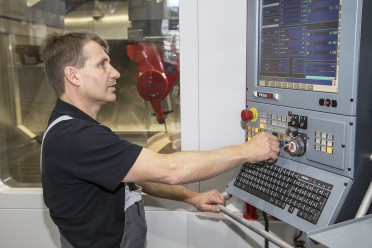
The CNC milling-machine operator Gerald Nothnagel has been working at Opel since 1993, and recently in the new center for high-speed milling machines.
Once where light metals were cast, high-quality design models are now milled.
FIVE MILLION EUROS INVESTED
Six high-tech milling machines are combined in the new center – from a giant full-size milling machine, in which future 1:1 vehicles are milled from hard plastic, to the mini mill, in which Opel brand emblems, for instance, are produced from metal. “Outstanding design is part of Opel’s brand essence. For things to stay that way, we invest in cutting-edge technology,” GM Executive Vice President & President Europe Neumann explains the project. Owing to the investment of five million euros, the creative geniuses can implement their ideas more quickly, precisely and dedicatedly.
EVIDENCE FOR A RETURN TO SUCCESS
It’s clear that Head of Design Mark Adams is satisfied: “The high-tech tools help us to optimize the entire development process from the first idea right through to the finished concept vehicle. They create design models defined by high quality, precision and efficiency.” Head of Opel Works Council Wolfgang Schäfer-Klug adds: “The new center ensures on-site employment. The investment is further evidence of Opel’s return to success.”
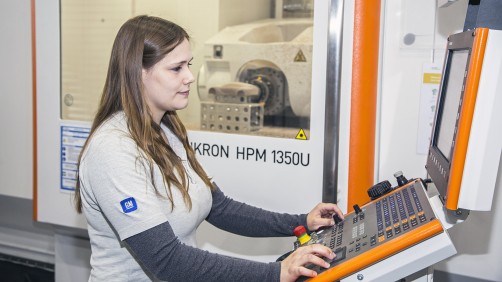
Stefanie Duinker is the choreographer of the Monza concept model.
NOT A QUESTION OF THE MATERIAL
When materials are chosen, the high-tech tools aren’t at all fussy. Whether aluminum, Styrofoam, Plexiglas or synthetic materials of varying hardness grades, what needs to be milled is simply milled. Richard Bolz, design operations director, supervised the new center’s construction and conversion. “The first models are formed from Styrofoam in order to optimize the proportions. The shaping of individual lines is refined with hard plastic models and the whole 1:1 model is finally produced in the full-size milling machine,” Bolz illustrates by example. Four of the six milling machines were newly acquired and the other two were already available. They were moved to the new center.
The premises were converted over the course of a year. In buildings H46/47, where light metals were cast up until 2000 and which had been idle since then, the center for high-tech tools emerged piece by piece. “A highlight was the installation of the full-size milling machine,” recalls the builder. The portal of the system alone weighs 13 tons. Yet the new center is a lot more than a bundle of machines. “Therefore, we have established our own milling organization for the Opel Design Center,” says Bolz. Some of the work that had been outsourced until now can now be dealt with here on site.
↑ Employees from the design team were invited a day after the official opening. This time in the full-size milling machine: the Opel Flextreme GT/E concept car exhibited at the Geneva Motor Show in 2010.
Richard Bolz, Director of GME Design Operations, is satisfied: He supervised the conversion. It took a year until a milling center arose from the former foundry. Opel invested five million euros to this end. →
The Opel Design Studio in Rüsselsheim can look back on a unique history spanning more than fifty years. As the first of its kind in the European automobile industry, it emerged as a magnet for vehicle designers from all over the world.
MODEL OF MONZA CONCEPT
While the official opening has ended and employees take a closer look at the machines – including heads of design operations from Australia, North and South America, Korea and Europe – the hard metal tip in the milling machine programmed by Stefanie Duinker keeps darting about boldly. “Already you can clearly make out what it’ll be,” says Duinker. “Obviously a Monza concept,” she adds. And how many working hours does the costly milling process take in order to produce the Monza concept? “About 14 hours,” the CNC operator reveals. And the hard plastic shavings kept flying into late evening.
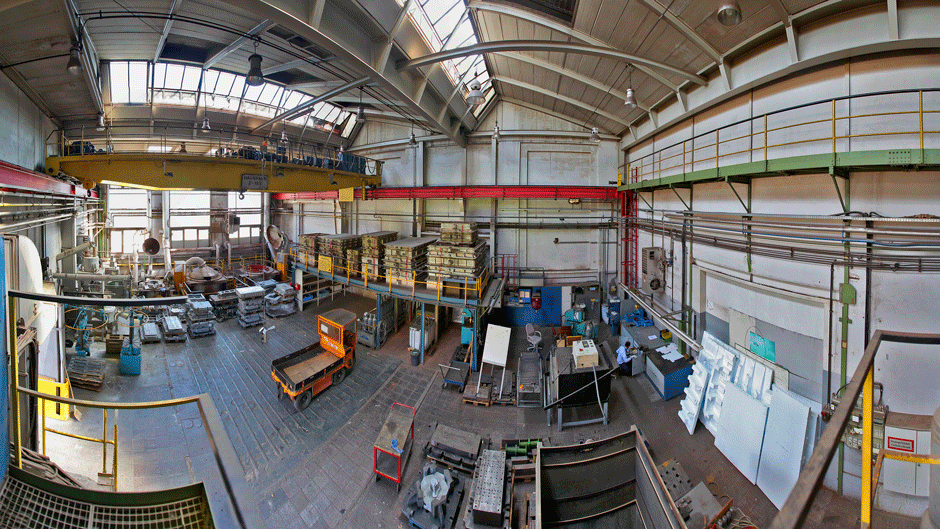
In four stages, from foundry to milling center: Marcus Weinert, photographer of the GME Design Center, documented the conversion process. On the premises of the current center for high-speed milling, light metals were cast up until the year 2000. Then the halls lay idle on the Rüsselsheim plant grounds. In the top left photos, the indoor crane is assembled. Using the crane, the models weighing up to two tons are lifted in and out of the full-size milling machine. In the top right photo, the indoor crane positions the 13-ton portal of the full-size milling machine.