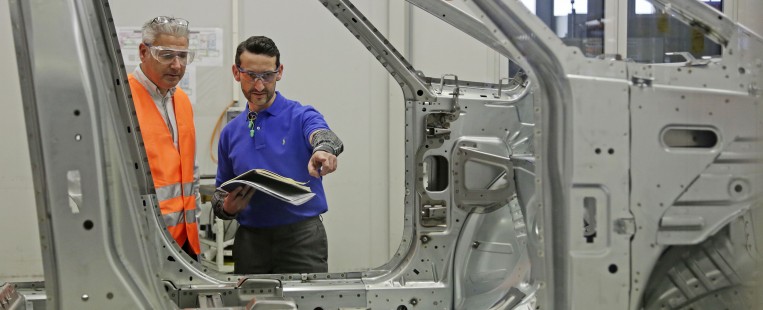
Taking a closer look: Neil Williams (right) and Karsten Faber don’t miss a thing.

A good listener: Manuela Kopainigg talks with employee Thomas Anicic in seat production.
Audits for the GM-GMS production system take place every year. However, nobody knows when exactly. Sometimes eight months go by, sometimes 11. What’s more, the audit is announced only a few days before it’s actually conducted. That was the case this year too. “We’re starting on Tuesday,” announced Agnieszka Tarala just one week beforehand. Tarala coordinates all of the European audits from the GM site in Gliwice. “We are deliberately only giving a very short period of notice,” explains Thomas Wedde, Head of GM-GMS and Training in Rüsselsheim. “At the end of the day, it’s about checking whether we actually apply GM’s global standardized production system in the plant every day. How could we prove how well we do it if we had the chance to specifically prepare for the audit?”
EVERYONE KNOWS WHAT THEIR TASK IS AND REMAINS CALM
What happens when an audit is looming? Does the team collapse with nerves? “What nerves?” says Thomas Wedde. He knows that he can rely on his organization. “The plant has an on-site team for each of the five GM-GMS principles and they work on implementation the whole year long. Each individual sub-item is also assigned to an employee who assumes responsibility for it. No stone is left unturned.” The Head of Training did not have to wait long to have his optimism confirmed. For example, take Thomas Anicic, team leader in door production. He spoke with Manuela Kopainigg in front of his section’s team notice board for about seven minutes. “I know what my tasks are and what to expect,” he explained afterwards in a relaxed manner. ↓
THE AIM OF GMS is to organize global manufacturing using a single production system.

Looking into every detail: Karsten Faber during ultrasonic testing of the shell.
Kopainigg traveled to Rüsselsheim from the GM plant in Aspern, Austria, where she is also responsible for GM-GMS. She was the ‘shadow’ on the international auditor team put together by Tarala. She was accompanied by external auditor Neil Williams, Head of Workplace Safety at Vauxhall in Ellesmere Port. The third member of the team was a local: Karsten Faber, who normally works as a shift manager in the pressing plant. Rüsselsheim is one of the GM plants where internal employees with the appropriate qualifications are authorized to conduct GM-GMS audits. External auditors take on an advisory role and are responsible for analyzing the results.
DIALOG AT EVERY LEVEL
A ‘shadow’ is an auditor who is still in training. Kopainigg’s first visit to Rüsselsheim was in this capacity. “I’ve had some very pleasant conversations here,” she summarizes. “I got the impression that the employees are very motivated and proud of what they do.” Together with her two colleagues, Kopainigg tested the extent to which GM’s employee involvement principle was fulfilled. ↓

Communicate: Internal auditor Karsten Faber and external auditor Neil Williams compare their impressions.
12
auditors from Rüsselsheim, Ellesmere Port, and Gliwice were on the case.
4
It took them four days to interview the employees at the production facility in Rüsselsheim.
89
The employees scored 89 out of 100 points – an excellent final result.

Evaluate carefully: Werner Dey, Stefan Moisa, Katrin Grandl and Dariusz Karaban (from left to right) discuss results.
There was a maximum of 20 points available for the employee involvement principle. No matter how informal the interviews seemed, the auditors made notes on all of the points covered after each one. The result justified the relaxed attitude of the Rüsselsheim team. They scored 19 points for the principle.
ROOM FOR IMPROVEMENT IS A PRINCIPLE IN ITSELF
At the same time, teams put together in the exact same way checked the degree of fulfillment of the other four GM principles: short lead times, built-in-quality, continuous improvement, and standardization. It goes without saying that production operations still need to run smoothly during a GM-GMS audit. After the on-site inspection, the whole team meets to carefully evaluate the results and make notes on what can be improved further. ↓

Expertise: The auditors must be able to assess whether employees can use the right gripping positions.
This was also relevant to the employees at Rüsselsheim, despite the fact that 89 percent is an excellent result. “We’ve just integrated the Zafira Tourer into our manufacturing line,” explains plant director Michael Lewald. “The auditors’ suggestions came at just the right time in order for us to further optimize our workflows and processes.” Even if a plant meets 89 percent of requirements and falls comfortably into the famous ‘green zone,’ continuously striving for improvement is a GM-GMS principle, too.↵
THE GM-GMS IDEA
All GM plants around the world should work with the same rhythm and to the same high quality standard – as far as this is possible. GM developed its Global Manufacturing System (GMS) to fulfill this requirement. Special audits are conducted once a year at every plant around the world to review the extent to which GMS is implemented. There are five principles: standardization of all processes, short lead times, built-in-quality, employee involvement, and continuous improvement.
Text: Eric Scherer, Photos: Alexander Heimann/Vollformat