- Motormontage-Bereich E von oben.
- Motormontage (v.l.n.r.): Johann Schmid, Ernst Fuchs, Gottfried Hahn.
- In Reichweite Teile entnehmen – das ist ergonomisch besser und effizienter (Johann Schmid).
- Das Team des Waste Elimination Workshops (v.l.n.r.): Peter Breitenfelder, Wilhelm Schütz, Jürgen Wolf, Günter Fritsch, Andreas Salomon, Peter Schmid, Herbert Förster, Christoph Karnthaler.
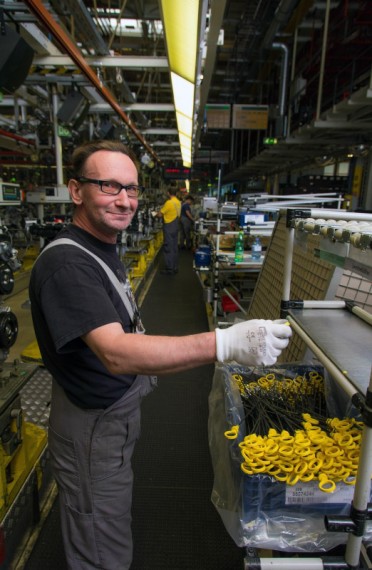
Die Kleinlastenträger (KLT) mit den Ölmessstäben werden jetzt um 90 Grad gedreht angestellt – das macht das Herausnehmen leichter (Hermann Stimmer).
Zur Vorgeschichte schickt Koordinator Kurt Henecker voraus: „Wir haben im Vorjahr mit einem weiteren ‚Optimierer‘-KVP die Performance beim Saugermotor verbessert. Beim Turbomotor haben aber noch ein paar Sekunden gefehlt.“
Gegen Betriebsblindheit
Um die Sache extra-gründlich anzugehen, besannen sich die KVP-Experten des Werks einer zuletzt vernachlässigten Methode: des Waste Elimination Workshops. Der Clou dieser Methode: Dem Team, das sich mit der Verschwendung befasst, gehören bereichsfremde MitarbeiterInnen sowie MitarbeiterInnen aus dem eigenen Bereich an.
Mitte März 2015 fand der dreitägige Waste Elimination Workshop statt. Mit KVP- und Prozessinformationen zur Auffrischung und einem ersten Lokalaugenschein in der Linie. Jedes der Teammitglieder erhielt ein bis zwei Stationen zugeteilt. Die Montage-Bereiche D und E standen im Mittelpunkt. Die wurden nun durchleuchtet; nach Aspekten der Ergonomie und der Arbeitssicherheit und vor allem im Hinblick auf die „7 Arten der Verschwendung“. Am dritten Tag wurden die Pillar Charts und die Dokumentationen an die neu definierten Abläufe angepasst. Die Ausbeute: 74 Ideen, von denen 22 gleich im Workshop umgesetzt werden konnten. Unnötige Bewegungen der MitarbeiterInnen wurden eliminiert; zum Beispiel bei der Zwischenlage des Zündmoduls oder bei der Entnahme des Ölmessstabs aus dem Kleinlastenträger/KLT oder bei der Rückführung von Leergut am Handarbeitsplatz E6. Oder es wurden Wege effizienter, kürzer gestaltet.
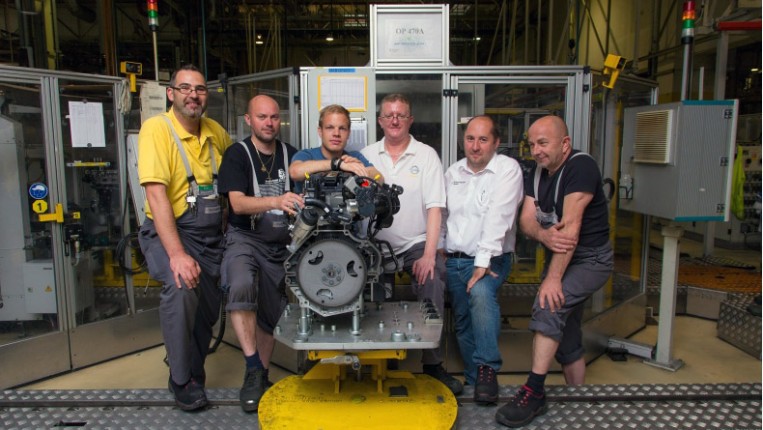
Das Team des KVP-Projekts „Optimierer 21“ (v.l.n.r.): Wilhelm Schütz, Ernst Bauer, Roman Trappl, Günter Fritsch, Christoph Karnthaler, Herbert Förster.
Insgesamt wurden im KVP-Projekt „Die Optimierer 21“ von den offenen 52 Ideen neun Verbesserungsinitiativen umgesetzt.
Der Vergleich macht sicher
Am 18. März übergab das Waste Elimination Workshop-Team die Stafette an das KVP-Projektteam. „Die Optimierer 21“ war an der Reihe. Die MitarbeiterInnen der Motormontage sind ja auf die Tradition ihrer KVP-Projekte besonders stolz und nennen sie allesamt „Optimierer“.
Basierend auf den Ideen des vorangegangenen Workshops ging es nun ans „Eingemachte“. Zuerst einmal wurden Kosten-Nutzen-Berechnungen angestellt, dann Montageversuche durchgeführt, danach die Linie ausbalanciert und die Ergonomie überprüft. Alles begleitet von immer neuen Messungen. Außerdem wurde auch noch der Bereich B/C der Montage mit berücksichtigt.
Die Summe aller Zykluszeiten wurde um fünf Sekunden reduziert, um die Arbeitselemente von Handarbeitsplatz C5 auf andere Handarbeitsplätze und Maschine OP 360 aufteilen zu können.
Weitere Detail-Beispiele: Dass der Einlasskrümmer jetzt nur mit einer Schraube vorangelegt wird, brachte 3,5 Sekunden. In der Station 360 wurde ein Andrücker zur Vermeidung von Nacharbeiten eingefügt.
Insgesamt wurden im KVP-Projekt „Die Optimierer 21“ von den offenen 52 Ideen neun Verbesserungsinitiativen umgesetzt.
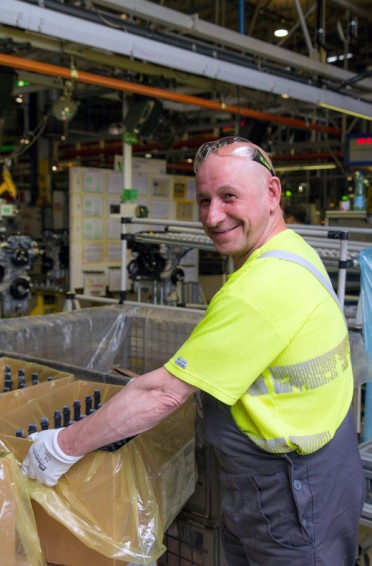
Lasten heben ist immer ein Thema für die Ergonomie (Erich Humpelstetter).
Text: Kristin Engelhardt, Fotos: Richard Tanzer
Stand Juli 2015