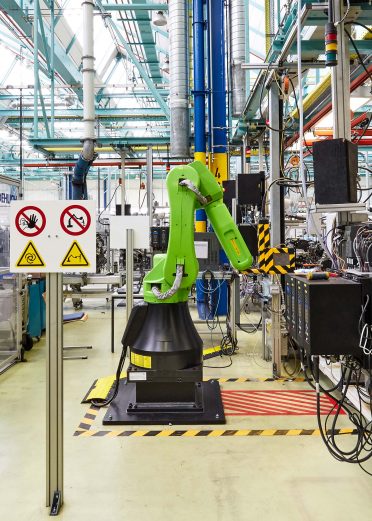
Bei der Konzeption eines solchen Roboters, der ohne Schutzgitter agiert, steht die Arbeitssicherheit besonders im Fokus.
Am Band in der Motorenmontage in Kaiserslautern verrichtet ein neuer Kollege seine Arbeit. Aber ihn zum Mittagessen in die Kantine einzuladen wird schwierig: Es handelt es sich um einen Industrieroboter, den ersten seiner Art bei Opel. Die Besonderheit: Der Roboter ist nicht eingezäunt – es gibt kein Schutzgitter.
„Hulk“ – so haben die Lauterer Kollegen den Roboter aufgrund seiner grünen Farbe getauft – gehört zu einer neuen Generation sogenannter kollaborativer Roboter, die auf Berührungen durch den Menschen reagieren. Kommt es zum Kontakt, stoppt die Maschine sofort. Möglich macht das ein Kraftsensor, der in den Roboterfuß integriert ist. Er überwacht die komplette Kinematik. Zusätzlich ist die Maschine mit einem weichen Material ummantelt: Kommt es zu einer Kollision, wird der Aufprall gedämpft.
FAKTOR ARBEITSSICHERHEIT
Bei der Auslegung einer derartigen Roboterzelle wird natürlich besonderes Augenmerk auf die Arbeitssicherheit gelegt. Es ist eindeutig festgelegt, welche Kräfte bei einem Kontakt mit dem Menschen auftreten dürfen. Dies wird bei der Abnahme im Detail getestet. Besonders kritische Situationen: Wenn der Roboter beispielsweise nach einem Bauteil greift oder wenn scharfkantige oder schwere Bauteile gehandhabt werden. „Daher lässt sich bei weitem nicht jede Anwendung kollaborativ umsetzen. Die neue Technologie erfordert in jeder einzelnen Anwendung zusätzliches Know-how und neue, konstruktive Lösungen. Ist das aber einmal geschafft, hat man eine sichere Produktionsanlage ohne die Notwendigkeit eines Sicherheitszauns“, erklärt Dr. Benjamin Kuhrke, Projektingenieur Neue Fertigungstechnologien.
HULK ALS PRODUKTIONSASSISTENT
Kollaborativen Robotern als Baustein der Industrie 4.0 wird eine große Zukunft vorausgesagt: Man erhofft sich durch sie eine flexiblere Automatisierung. Und eine Entlastung der Mitarbeiter bei ergonomisch kritischen Tätigkeiten – der Roboter als Produktionsassistent. Im Werk Kaiserslautern kommt der Roboter zum Einsatz, um den Auslasskrümmer am Motor auf Drehmoment zu verschrauben. Das leistet in diesem Fall einen Beitrag zur Produktivität. „Es entlastet aber auch die Kollegen, da es sich um einen kräftezehrenden Montageschritt handelt“, sagt Axel Schaaf, Gruppenleiter im Manufacturing Engineering im Werk. Wesentliches Ziel des Piloten sei es gewesen, so Dr. Benjamin Kuhrke, „grundsätzliche Erfahrungen hinsichtlich der Arbeitssicherheit und der Umsetzung zu machen, um für weitere Anwendungen den Weg zu ebnen.“
Der Roboter, der in Kaiserslautern im Einsatz ist, ist ein Fanuc Roboter Cr-35iA mit einer Traglast von 35 Kilogramm. Im Laufe des Jahres wird Fanuc das Produktspektrum in diesem Bereich mit Robotern mit einer Traglast von drei, vier und sieben Kilogramm erweitern.
Der Bereich Fertigungstechnologieentwicklung der ME unter der Leitung von Frau Dr. Petra Krammer hat das Projekt initiiert und maßgeblich vorangetrieben. Umgesetzt wurde das Projekt von einem Opel-Team aus dem zentralen Manufacturing Engineering (ME) in Rüsselsheim sowie der lokalen ME, der Arbeitssicherheit und der Instandhaltung im Werk Kaiserslautern.
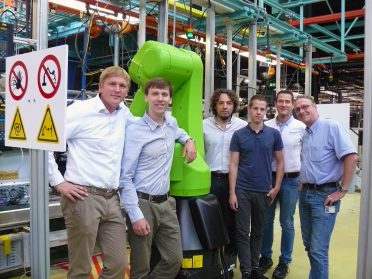
↑ Das Projektteam (von links): Dr. Benjamin Kuhrke (Projektingenieur Neue Fertigungstechnologien ME S&P), Daniel Schröter (Doktorand Mensch-Roboter-Kollaboration ME S&P), Philipp Neupert (Instandhaltung LDE Linie, Werk Kaiserslautern), Benjamin Baecker (ME Cylinder Head Assembly CSS, Werk Kaiserslautern), Axel Schaaf (Group Leader Manufacturing Engineering LDE, Werk Kaiserslautern) und Joachim Blochowitz (Process Engineer, Engine and Cylinder head Assembly – ME Powertrain).
Stand Juli 2016