Transformers Award
Projekt ograniczania gazu i spalin został odznaczony nagrodą Transformers Award. Wyróżnienie to przyznawane jest przez centralę General Motors najbardziej kreatywnym pomysłom spośród wszystkich fabryk GM na świecie. Proces wyłonienia najlepszych z najlepszych przebiega dwuetapowo. Najpierw fabryki samodzielnie decydują o tym, które z projektów w obrębie swoich jednostek uważają za szczególnie godne uwagi. Potem propozycje wysyłane są do centrali w Stanach Zjednoczonych, gdzie specjalnie wyłoniona kapituła wybiera te najciekawsze i najbardziej pomysłowe.
Zdobyta nagroda to kolejny dowód na to, jak innowacyjną, kreatywną i wartościową fabryką jesteśmy na mapie zakładów GM.
100 procent – taka jest efektywność odzysku niewykorzystanej farby z głównych linii zasilających za pomocą „świnek”
200 litrów – taką pojemność ma standardowy zbiornik lakieru używany w procesie malowania
Wygląda niepozornie – kawałek owalnej gumy z lekkimi zaokrągleniami na obu końcach. Długość – 3 centymetry, średnica – 12 milimetrów.
– To właśnie „świnka” – tłumaczy Wojciech Więckowski, inżynier ME z lakierni. – Genialna w swojej prostocie. Ale właśnie dzięki niej udaje się zaoszczędzić sporo farby.
„Świnka” jest kluczowym elementem technologii pozwalającej na błyskawiczną zmianę koloru używanego w kabinie lakierniczej.
– To małe coś trafia do węża lakierniczego – wyjaśnia Wojciech. – Przy ładowaniu farby jest przepychane przez nią i nie zakłóca procesu malowania. Gdy jednak trzeba zmienić kolor, podajemy do węża z drugiej strony sprężone powietrze i „świnka”, już wracając, pozwala odzyskać pozostałą jeszcze farbę, pchając ją przed sobą.
Po takim czyszczeniu można spokojnie podłączyć nowy zbiornik z innym kolorem i malować dalej. Cała zmiana zajmuje nie więcej niż 30 minut. To kilkadziesiąt razy krócej, niż w przypadku tradycyjnych systemów.
– W nich proces czyszczenia instalacji trwa nawet dwa dni – mówi Grzegorz Jezusek, inżynier procesu z lakierni. – Widać więc, jak ogromna jest oszczędność czasu.
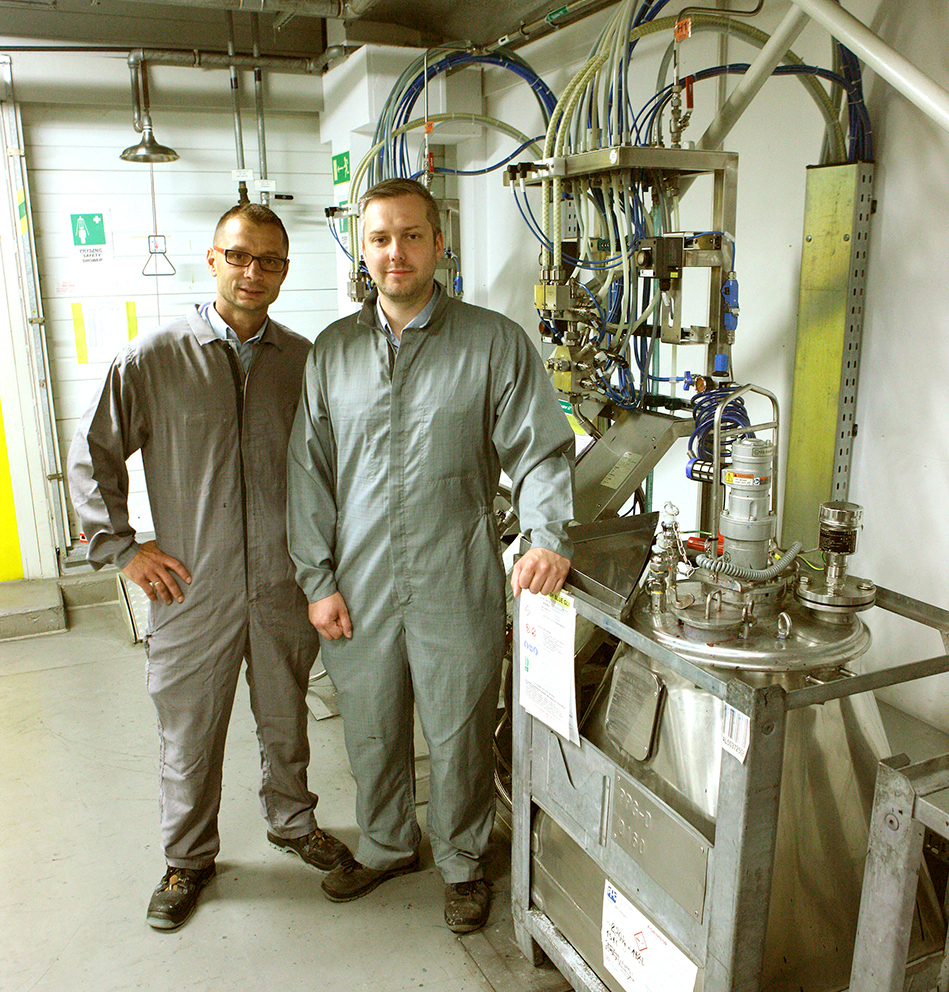
Od lewej: Grzegorz Jezusek i Wojciech Więckowski przy „śwince”.
Ale nie tylko czasu. Standardowe czyszczenie wiązało się z dużą stratą farby, która zostawała w instalacji i była wypłukiwana. Przy „świnkach” to o ponad dwadzieścia pięć razy mniej .
– Jest jeszcze jedna, kluczowa zaleta – opowiada Grzegorz. – Klienci szukają dziś większej gamy kolorystycznej pojazdów. A my bez problemu w szybkim czasie jesteśmy w stanie pomalować krótką serię pojazdów, a zaraz potem kolejną, w zupełnie innym odcieniu.
W języku lakierników mówi się o kolorach „highrunnerowych” i „lowrunnerowych”. Te pierwsze to najpopularniejsze: biały, czarny czy czerwony. Te drugie już same nazwy mają oryginalne, np.: true blue czy sunny melon.
– Niektórymi z nich pokrywamy tylko 10 samochodów w skali tygodnia, ale o każdego nabywcę trzeba walczyć – zauważa Wojciech. – Łącznie, przy obecnych możliwościach i starego, i nowego systemu jesteśmy w stanie zaoferować 20 kolorów.
Za systemem (zwanym z angielska Easy Pig) poszły i udogodnienia dla pracowników lakierni. Zainstalowany został panel, pozwalający team leaderowi na wprowadzanie ustawień parametrów podawania farby, bez konieczności biegania i korygowania każdego stanowiska.
– Udało się zaprogramować ustawienia dla poszczególnych typów farb, bo każdy kolor ma inne właściwości, np. gęstość i innego trzeba ciśnienia, by go podać do kabiny – wyjaśnia Wojciech. – Jak czerwony ma 1,8 bara, to srebrny już powiedzmy 2,2.
„Świnka” i panel sprawdzają się więc świetnie, ale specjaliści z lakierni szukali dalszych możliwości oszczędzania. Niedawno zabrali się za zużycie energii i gazu w suszarkach lakierni.
– Z powodu przerw produkcyjnych linii lakierniczych piece Primera oraz Top coat nie mają 100 % wypełnienia – wyjaśnia Marek Dyrcz, kierownik grupy procesowej – i właśnie w takich momentach dochodziło do największych strat energii. Wzięliśmy pod lupę powodujące to czynniki i okazało się, że jest rozwiązanie.
Na dodatek takie, które nie wymagało żadnych inwestycji w materiały czy nowe urządzenia. Wystarczyło połączyć czujnik temperatury na wylocie w kominie suszarki z głównym wentylatorem.
– Ustawiliśmy poziomy temperatur w zależności od ilości karoserii i teraz czujnik, jeśli dostanie odpowiednią informację, przekazuje ją do wentylatora, którego moc i tempo pracy jest korygowane. Więcej karoserii to więcej energii, mniej – powoduje od razu zmniejszenie wartości.
Ten prosty manewr pozwolił wystartować z projektem już pod koniec ubiegłego roku .Dziś na dobre widać, jakie przyniósł korzyści.
– Przede wszystkim ekologiczne – zauważa Marek. – System znacząco wpływa na redukcję emisji dwutlenku węgla. Do tego przynosi duże oszczędności mediów.
Plan wprowadzenia zmian został zaakceptowany na poziomie światowym GM w ramach tzw. projektu Transformers. I bardzo się spodobał.
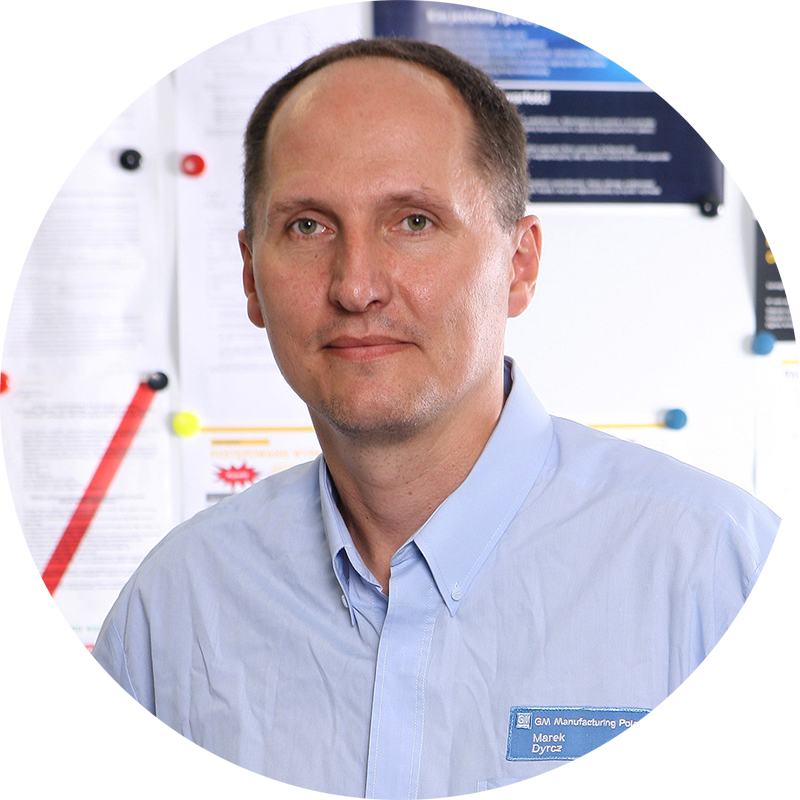
Marek Dyrcz