Auf dieses Datum haben sich die Eisenacher Kollegen seit Monaten intensiv vorbereitet: Am 28. August war offizieller Produktionsstart des Opel Grandland X. Nach dem Produktionsende von ADAM und Corsa Anfang Mai wurden die alten Anlagen in weiten Teilen abgebaut, neue Technik für das kompakte SUV hat Einzug gehalten. Etwa 200
Opelaner hatten den Umbau unterstützt, insgesamt wirkten über 1.200 Mitarbeiter von Fremdfirmen aus mehr als 20 Nationen an dem Projekt mit. Was ist neu, was ist anders? Die Opel Post sprach mit fünf verantwortlichen Managern aus den Bereichen Rohbau, Lackiererei, Fertig- und Endmontage, Qualität sowie Logistik.
Rohbau
Fertigung geht in die Tiefe
Am 30. April ging es los: Anlagen, Förderer und Roboter wurden im Rohbau demontiert. Bis auf die Hauptlinie wurden alle Anlagen innerhalb von zwölf Wochen, auch dank der Hilfe von unseren Mitarbeitern, umgebaut. Grund der umfangreichen Umstellung: Statt einer Kleinstwagenkarosse fertigen wir nun eine SUV-Karosse. Die Bodenstruktur ist eine völlig andere, die Roboter wurden entsprechend umprogrammiert. Auch die Fertigungstiefe hat sich verändert. Beim ADAM haben wir ausschließlich Vordertüren gefertigt, jetzt sind es Vorder- und Hintertüren sowie die Haube – und die ist aus Aluminium, was eine neue Herausforderung für uns ist, gerade was die Oberflächenbehandlung angeht. Neu ist auch, dass wir jetzt das Dach und den Vorderwagen Laserlöten, dafür haben wir unsere Mitarbeiter intensiv geschult. Wir haben bereits eigene Karossen gebaut und die Prozesse getestet, jetzt erhöhen wir die Stückzahlen. Größte Veränderung nach der Umstellung: die Eigenverantwortlichkeit steigt deutlich.
Kai Stephan
Manager Rohbau
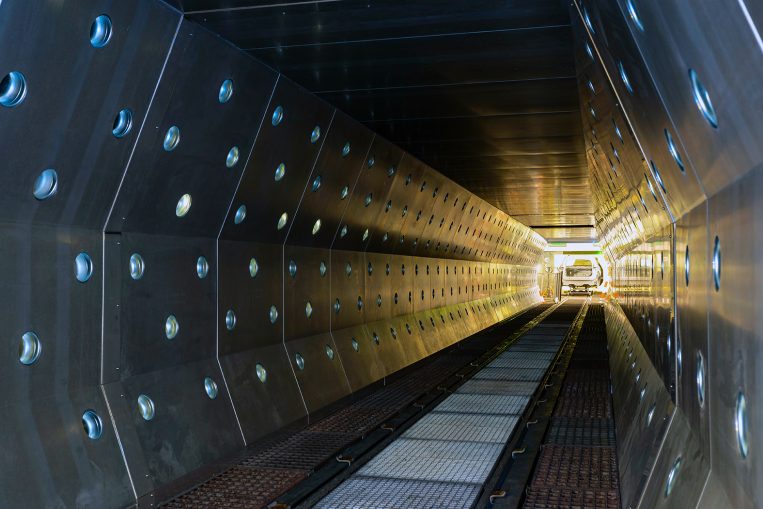
Effizient: Dank des neuen Systems entfällt ein aufwendiger Schritt, denn in dieser Anlage werden Basislack und Klarlack gemeinsam getrocknet.
Lackiererei
Umweltschutz wird großgeschrieben
Arto Savolainen
Manager Lackiererei
Es ist der bisher für uns grundlegendste Umbau: Wir haben die produktionsfreie Zeit intensiv genutzt, um wettbewerbsfähige Technik und Technologien zu installieren. Das zieht natürlich auch neue Prozesse und Strukturen nach sich. Wir haben beispielsweise schrittweise ein neues Lackierungsverfahrens eingeführt, den sogenannten 4-Wet Prozess. Er wird zu einer deutlichen Reduzierung von Emissionen führen. Dank des Verfahrens entfällt die separate Grundlacktrocknung. Stattdessen gibt es nur noch einen Trocknungsprozess für Basislack 0, Basislack und Klarlack. Das schont die Umwelt. Und da zusätzlich die Grundlackauswaschung entfällt, senken wir den Wasserverbrauch deutlich. Darüber hinaus reduziert sich durch die Automatisierung bei der Basislack- und Klarlackapplikationen der Materialverbrauch um bis zu 30 Prozent.
Fertig- und Endmontage
Alles auf Neuanfang
Wenn ein neues Modell kommt, passen wir üblicherweise die Anlagen an – und los geht es. Nicht dieses Mal: Aufgrund des Architekturwechsels ist alles neu! Zunächst musste alles abgebaut werden – von den Fördereinrichtungen, über die Hochzeit bis hin zu den Befüllanlagen. Parallel haben wir die neuen Anlagen an anderer Stelle aufgebaut. Steuerung, Software, Materialanlieferungssystem, Arbeitstakte und die Zuordnung der Mitarbeiter, Bereichsgrenzen, Sicherheitsstandards – alles wurde optimiert. Größter Unterschied zu vorher: Wir werden künftig an der Linie nicht mehr manuell eingreifen. Denn das PSA-Konzept ist sehr geradlinig und strukturiert und lässt keine Abweichungen zu. Die Werkzeugprüfungen sind deutlich strenger, jede kritische Operation wird systematisch überwacht und jedes Bauteil zuvor auf seine Richtigkeit gescannt. Wir stellen uns gerne dem Neuen – diese neue Plattform ist eine gute Investition in die Zukunft. Außerdem können wir relativ einfach weitere Varianten auf der Linie integrieren, wie etwa den Opel Grandland X Plug-In-Hybrid.
Thomas Steinmetz
Manager Fertig- und Endmontage
Qualität
Mitarbeiter stehen bereit für den Neuen
Renno Kallenbach
Manager Qualitätsbereich und Reparatur
Wenn das Auto vom Band läuft, sind wir vom Qualitätsbereich an der Reihe. Für den Grandland X haben wir die Inspektions- und Prüfprozesse analog der Fahrzeugarchitektur und der IT modifiziert: Spureinstellung, Scheinwerfereinstellung sowie die Testeinstellungen für die Radar- und Frontkamera. Ein neues Abluftsystem für die Bodenabsaugungen leitet jetzt die Abgase berührungslos beim Starten des Fahrzeuges ab. Für den dynamischen Vehicle-Treiber, der auf Rollen das Fahren auf der Straße simuliert, wurden ebenfalls Spurweite, Bremsentest und Software modifiziert. Im Reparaturbereich haben wir neues Spezialwerkzeug angeschafft und alle Mitarbeiter trainiert. Zudem wurde ein neues Erfassungstool mit dem Namen QUALIF für den Qualitäts- und Fertigungsbereich installiert, das den Qualitätsstand der Fahrzeuge in Sachen Schraub-, Scan- und Befülloperationen widerspiegelt.
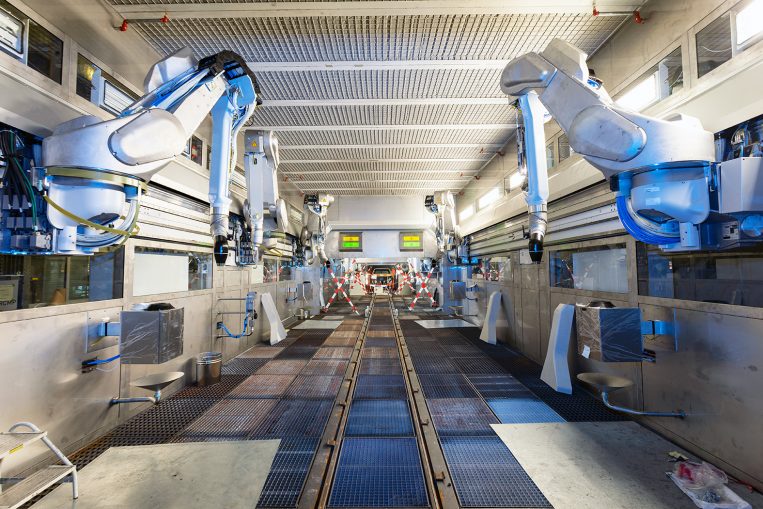
Nicht mehr manuell: Die Lackierung des Innenraums übernehmen künftig diese neuen Roboter. Während des Lackierprozesses werden die Vorder- und Hintertüren sowie die Motorhaube durch Roboter geöffnet und wieder geschlossen.
Logistik
Geliefert wie verbaut
Eigentlich ist nur die Hülle stehengeblieben: Wir haben innerhalb von zwei Monaten das komplette Innenleben im Gebäude E100 umgebaut. Die gesamte Logistik bestehend aus Bestellsystem, Lagersystem, Liefersystem und IT wurde auf das PSA-System umgestellt. Das heißt für uns: Wir bestellen Material beim Lieferanten exakt analog zur Aufbausequenz in der Fertig- und Endmontage. Ein Auftragspaket umfasst zehn Tage. Die Materialanlieferung geht nach der Kontrolle je nach Aufbausequenz für einen Zwei-Stunden-Takt zuerst in das sogenannte Cross Doc – hier können für 800 Fahrzeuge Kleinteile gelagert werden. Im „Supermarkt“ werden anhand eines „Einkaufszettels“ die Teile nach Bedarf geladen und nach Anforderung an die Linie geliefert. Da wir nach Bausequenz liefern, ist die Einhaltung der richtigen Aufbaureihenfolge sehr wichtig. Darauf müssen wir uns vom Empfang bis an die Linie einstellen. Neu ist auch der Supplier-Park: Hier montieren unsere Dienstleister in unmittelbarer Nähe zur Fertigung Komponenten wie Rückwandklappe, Himmel mit Kabelsätzen und die Auspuffanlage vor. Das spart Wege und Transportkosten.
Uwe Bosecker
Logistik-Manager
September 2019