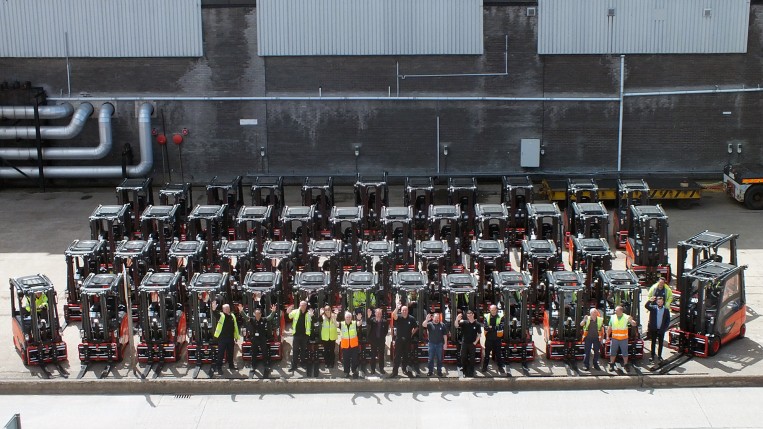
In tight formation: The new fleet of forklifts at the back of the pressing plant in Ellesmere Port.
The forklifts in Ellesmere Port are now running on electricity.
This makes vehicle traffic at the plant safer and
more environmentally friendly while also saving money.
That’s because the old gas-powered forklifts have now been replaced by an all-electric fleet. Even though these are already in general use at GM plants across Europe, “going from gas-powered to electric forklifts posed a tremendous challenge in England and required a lot of advanced planning,” Karsten Wilke explains, who, as Regional Coordinator GME Material Handling Equipment, is in charge of supervising the project for the Facility Management division headed up by Wolfgang Rentsch. A lot of money was spent making the transition to electric forklifts. The 71 new forklifts have been purchased outright, whereas the old ones were leased. “We were able to demonstrate that buying them was less expensive than leasing them from a long-term perspective. In two to three years they will have fully paid for themselves,” says Karsten Wilke.
There were other reasons that supported the switch from gas to electric forklifts. Since the ones in use at Ellesmere Port are operated almost entirely indoors in an enclosed plant, it is not only environmentally friendly but also helps protect the health of employees by having zero-emissions vehicles that run on electricity not gas.
The new batteries found on the forklifts are fast-charge batteries. This is vital due to the special two-shift model in use in Ellesmere Port. That’s because the forklifts are in service for 19 hours at a time. However, thanks to the fast-charge batteries, even quick breaks can be used to charge them. Plus, the five hours at night where the forklifts at the plant are not in operation are more than enough to fully charge them.
It is also worth noting that the batteries are charged inside the enclosed plant, meaning the forklifts no longer have to go outside to charge up. “That in turn has the advantage that they do not carry dirt into the plant anymore,” Karsten Wilke adds. “This makes everything look nicer, reduces cleaning costs, and helps improve occupational safety.” On a further note, the main charging station was installed in a part of the plant where skeleton construction used to take place. Everything was already in place in terms of power. “This allowed us to create the infrastructure needed to charge the new forklift batteries for very little money.”