How many ways can you design an ADAM? 500,000 or even over a million? It really says something when someone like Torsten Steinert stops thinking about the number of different versions of the ADAM and ADAM ROCKS models that can leave the Opel plant in Eisenach in order to satisfy all of our customers. It’s not because Steinert has lost track of his area of responsibility. Quite the contrary, the project coordinator is familiar with every last detail of the work processes and figures that come into play when manufacturing the ADAM models. But the variety of options for chassis and roof colors combined with dozens of special features and extras stretches into the hundreds of thousands at the very least. This results in different designs making it out onto the streets: “You rarely set eyes on a vehicle from Eisenach with the same features more than once,” says Steinert with conviction. When it comes to the ADAM and now the ADAM ROCKS, too, every customer is a designer.
The high level of customization on offer for the ADAM and ADAM ROCKS models have never before been seen in the automotive industry, says Torsten Steinert. This begs the question: How do the employees in Eisenach manage to do it? Flexibility is the name of the game. Material and production flows are adapted to customer requirements. To gain a better understanding of the new manufacturing concept, Opel Post took a look at three areas: the paint shop, logistics, and the customization zone.
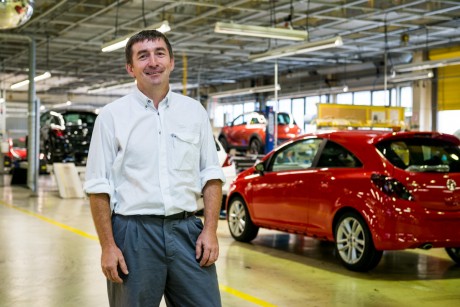
The high level of customization on offer for the ADAM and ADAM ROCKS models have never before been seen in the automotive industry, says Torsten Steinert.
Stop 1: The Paint Shop
The paint shop’s multi-story hall complex has an output of 37 vehicles per hour. Most feature a two-color paint job. Still, two out of three customers like to change it up. If this is the case, the chassis pass through the painting process twice. Markus Moewe, Launch Team Leader, explains exactly how this works: “After the base color is applied, the doors and tailgates are dismantled. Employees then manually mask the chassis, so that on the second pass through, only the desired areas are painted.” The complex manual work takes place on a masking line specially developed for ADAM production. So what are the essential elements of this special procedure? “Steady hands are absolutely essential. The masking has to be 100 percent accurate,” says Moewe. As Launch Team Leader, he is responsible for recording, troubleshooting, tracking, and solving any problems that occur during the launch progress.
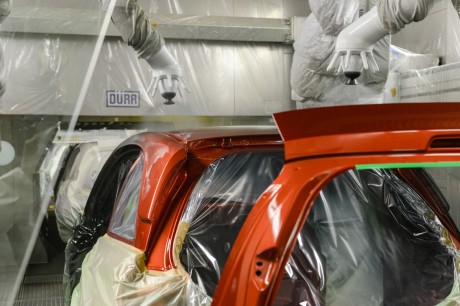
The paint shop’s multi-story hall complex has an output of 37 vehicles per hour.
Stop 2: Logistics
Normally, the components to be installed are available on the line. The employee reaches into a container, grabs the gear knob, and then installs it. However, the gear knob for the ADAM and ADAM ROCKS models isn’t just available in different colors, it comes with different stitching, with plastic, synthetic leather and leather components, in five- or six-gear mode, and for manual or automatic transmission. Is it possible to store a range like this on the production line, you ask? No, it’s not. Instead, there are 11 small component depots, known as SPS (set part system) stations, located between the assembly lines. The components to be installed for each individual vehicle are collected here.
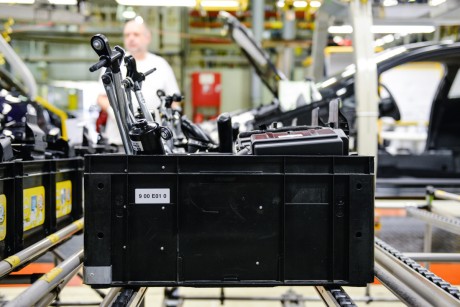
The components placed in the box are necessary for assembling a specific vehicle.
In concrete terms, employees like Stefan Pottschien load up a black box at the SPS station. The components placed in the box are necessary for assembling a specific vehicle later on and include interior components such as decorative trims for the dashboard or the gear knob. “The contents of the box are perfectly matched to the vehicle. We draw from an enormous pool of components,” says Pottschien. He picks up a filled SPS box that will be placed a few meters further down the assembly line at the right vehicle. Torsten Steinert summarizes the SPS principle as follows: “It allows us to save a lot of space on the line and avoid any mix-ups. This way, we can deliver top quality.”
Stop 3: The Customization Zone
When an ADAM rolls off the line, it has its own individual color and unique interior. But that’s not all. Every third ADAM that leaves the line also stops by the customization zone. “This is where the final touches are made,” says Steinert, pointing to an area the size of two basketball courts. The on-site team customizes up to 80 vehicles per shift, for example, with application films.
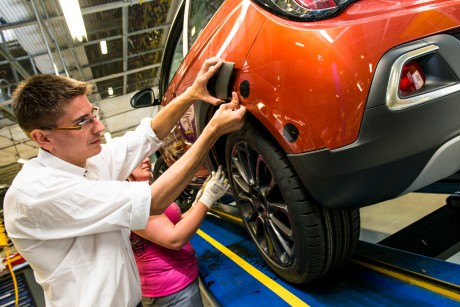
Every third ADAM that leaves the line also stops by the customization zone.
Anyone wandering around this area is bound to bump into team representative Dieter Eimer. Right now he’s applying an application film to a magma red Corsa – two stripes along the front section and the roof. “We satisfy this kind of individual customer request here rather than on the line,” says Eimer. Close by, an ADAM ROCKS is getting the robust ‘offroad’ look. He’s installing additional door sills and paneling for the bumper and wheel cases. Torsten Steiner is very fond of this look, particularly the combination of the arden blue roof and cream white chassis. “It’s my favorite combination – at least it is right now,” he says.