Employees at the Eisenach plant have been making intensive preparations for months. Finally, the production of the Opel Grandland X has officially started on August 28, and the work to get everything ready has been ramping up over the past few weeks. The end of production of the ADAM and Corsa at the beginning of May saw much of the old machinery dismantled, to be replaced by new equipment. Around 200 Opel employees
have been working on the conversion, with a particular focus on maintenance and mechanical engineering work. A total staff of more than 1,200 employees from external firms based in more than 20 countries have also been involved in this enormous project. Opel Post spoke to five of the managers responsible for production, representing the Bodyshop, Paint Shop, Final Assembly and Finishing, Quality Control, and Logistics departments.
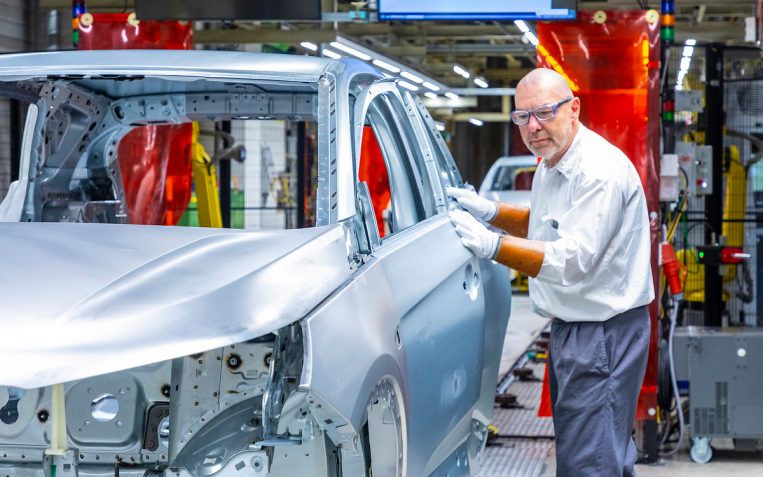
On its way to Russia: Opel CEO Michael Lohscheller announced that the Grandland X manufactured in Eisenach will be the spearhead of the comeback on the Russian market this year.
Bodyshop
More Manufacturing Under One Roof
“It all started on April 30. That was when the equipment, conveyors and robots were dismantled in the Bodyshell department. Apart from the main production line, all the other equipment was converted within twelve weeks, not least thanks to the efforts of our employees. Why are we making these sweeping changes? Because instead of building a small car chassis, we’re going to be building an SUV chassis. The floor structure is totally different, so the robots have been re-programmed accordingly. The level of manufacturing we do in-house has changed, too. With the ADAM we were only manufacturing the front doors. Now we’re doing the front doors, rear doors, and hood. And the hood is made of aluminum, which is a new challenge for us, especially as far as surface treatment is concerned. Something else that’s new is that we are now laser-soldering the roof and the front doors; we have had to provide our employees with some intensive training on that. We’ve already built a few chassis and tested the process; now we’re increasing the numbers before starting in earnest. What will be biggest change be after the conversion? The level of individual responsibility will be much higher.”
Kai Stephan
Bodyshell Manager
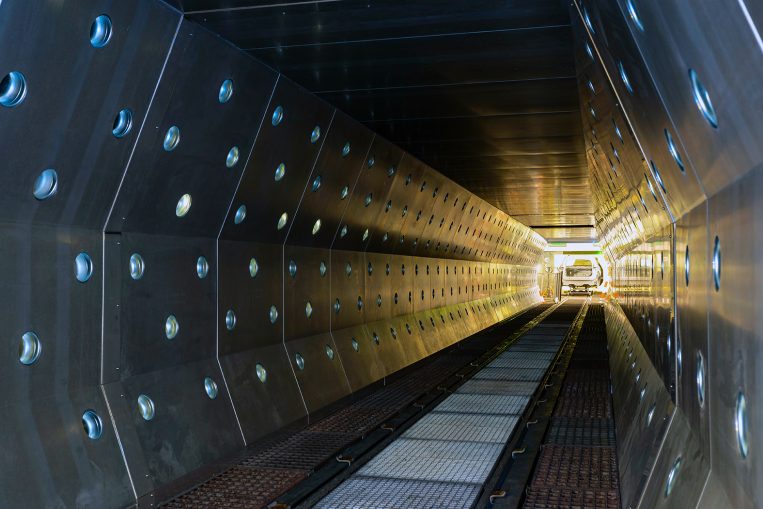
Efficient production: Thanks to the new coating system, a time-consuming drying step is no longer necessary. This is good for the environment.
Paint Shop
Environmental Protection Is a Top Priority
Arto Savolainen
Paint Shop Manager
“It’s the biggest conversion we have done so far. We spent the time while production was shut down working hard to install the equipment and technology to keep us competitive. Of course, doing that also brings new process and structures with it. For instance, we gradually introduced a new paint procedure, known as the ‘4 wet process.’ It will bring a major reduction in our emissions. The procedure removes the need to dry the primer separately. Instead, we have just one drying process for base coat 0, base coat, and clear coat. That’s good for the environment. And because we don’t need to wash out the primer either, we’ve also reduced our water consumption significantly. On top of all that, automating the process for applying the base coat and clear coat reduces our materials consumption by up to 30 percent.”
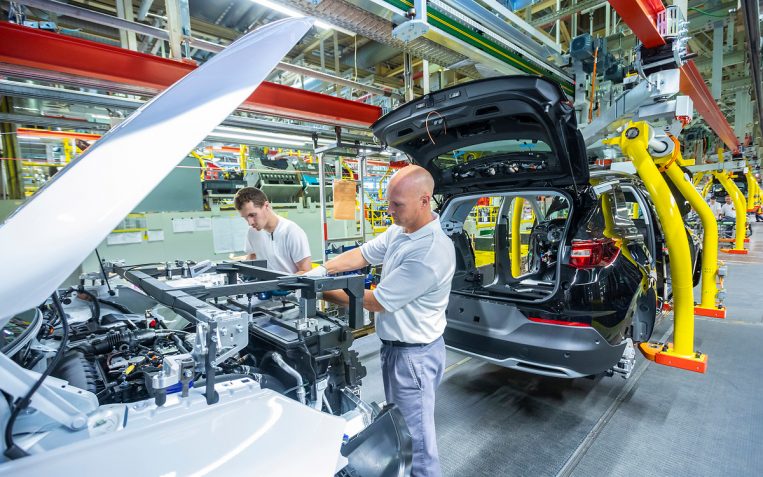
The most extensive conversion in the history of the plant: The former small car plant in Eisenach is now an SUV plant. All processes have been converted to the flexible EMP2 platform of the Groupe PSA. About 200 Opel employees and more than 1,200 employees from external companies from more than 20 nations participated in the conversion.
Final Assembly and Finishing:
Starting Over
“Usually when a new model comes along, we adjust the equipment and away we go. Not this time. The architecture has changed, so everything is new! First of all we had to dismantle everything – from the conveyor units to the marriage and filling equipment. We assembled the new equipment in parallel at another location. Control systems, software, the materials delivery system, work cycles and the way employees are assigned to different jobs, the boundaries of the different departments, the safety standards – you name it, we’ve optimized it. The biggest difference from before is that we’ll stop intervening manually on the line. That’s because the PSA concept is very simple and structured, so there is no room to deviate from it. The tool inspections are significantly more stringent than before, every critical activity is supervised, and every part is scanned before it is used to make sure it is in perfect condition. We are very happy to adapt – this new platform is a good investment for the future. We can integrate other variations into the production line fairly easily, too, like the Opel Grandland X plug-in hybrid.”
Thomas Steinmetz
Final Assembly and Finishing Manager
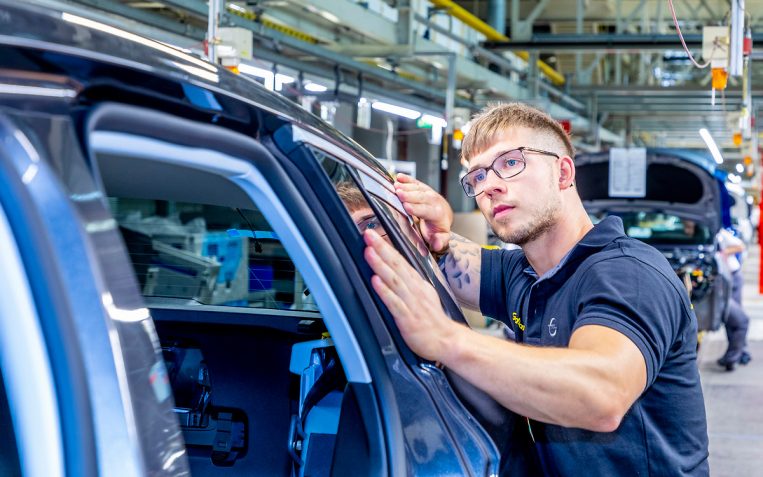
The Grandland X is a success story: More than 160,000 units of the SUV haven been sold since its market launch. Compared to the same period last year, sales in 2019 have increased by more than 40 percent.
Quality Control
Ready for the New Arrival
Renno Kallenbach
Quality Control and Repairs Manager
“As soon as the car comes off the production line, it’s time for us in Quality Control to get to work. We have modified our inspection and checking processes to take account of the new vehicle architecture and IT. They cover wheel alignment, headlight installations, and the test settings for the radar and front cameras. There’s a new ventilation system for floor extractions that automatically diverts the exhaust gases away when the vehicle is started. We’ve changed the lane width, the brake testing procedure, and the software for the dynamic vehicle drive systems, which are tested on a rolling road to simulate real-life driving. We’ve acquired a new special tool in the repairs department and trained all our employees on how to use it. On top of all that, we’ve installed a new data collection tool called QUALIF for the quality control and manufacturing department. It tests the quality of the vehicles in terms of how well the screwing, scanning, and filling have been done.”
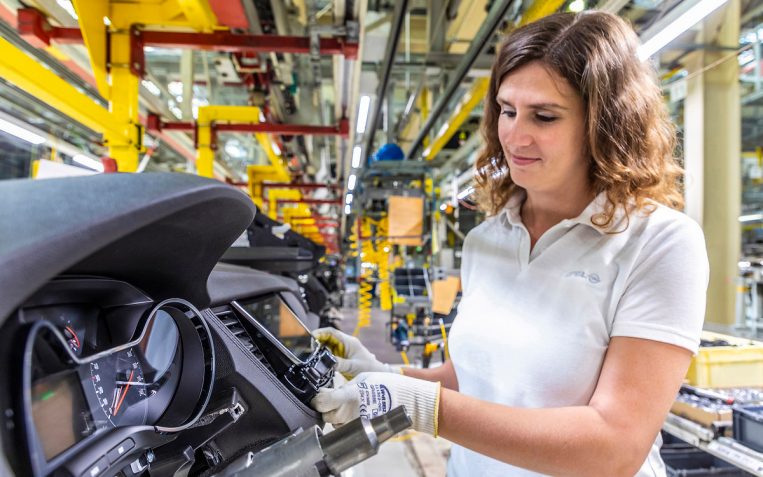
Everything is new: The delivery of the components and the production on the line are now even more closely interlinked.
Logistics
Designed to Deliver
“Actually, the shell’s the only thing that’s still here. Within two months we’ve changed the whole way the things in E100 work. The whole logistics department, including the ordering system, storage system, delivery system, and IT system, have all been converted to PSA’s system. From our point of view, that means we order materials from our supplier to exactly match the assembly sequence in Final Assembly and Finishing. An order package takes ten days, from start to finish, to complete. Depending on the assembly sequence, once deliveries of materials have been inspected they go into what we call the ‘Cross Doc’ for a two-hour cycle – it can hold enough small parts for 800 vehicles. The parts are then loaded from this ‘supermarket’ as required using a ‘shopping list’ and delivered to the line as needed. It’s very important to make sure everything is assembled in the right order since we are delivering according to the assembly sequence. Everyone has to adapt to that, from receiving to the production line. The supplier park is new, too. This is where our service providers put together components like tailgates, headliners with all the accompanying cables, and exhaust units, right next to manufacturing. That shortens supply lines and saves on transport costs.”
Uwe Bosecker
Logistics Manager
September 2019